Technology
THE SYNTHEC FUELS PLANT VIDEO
Feedstocks
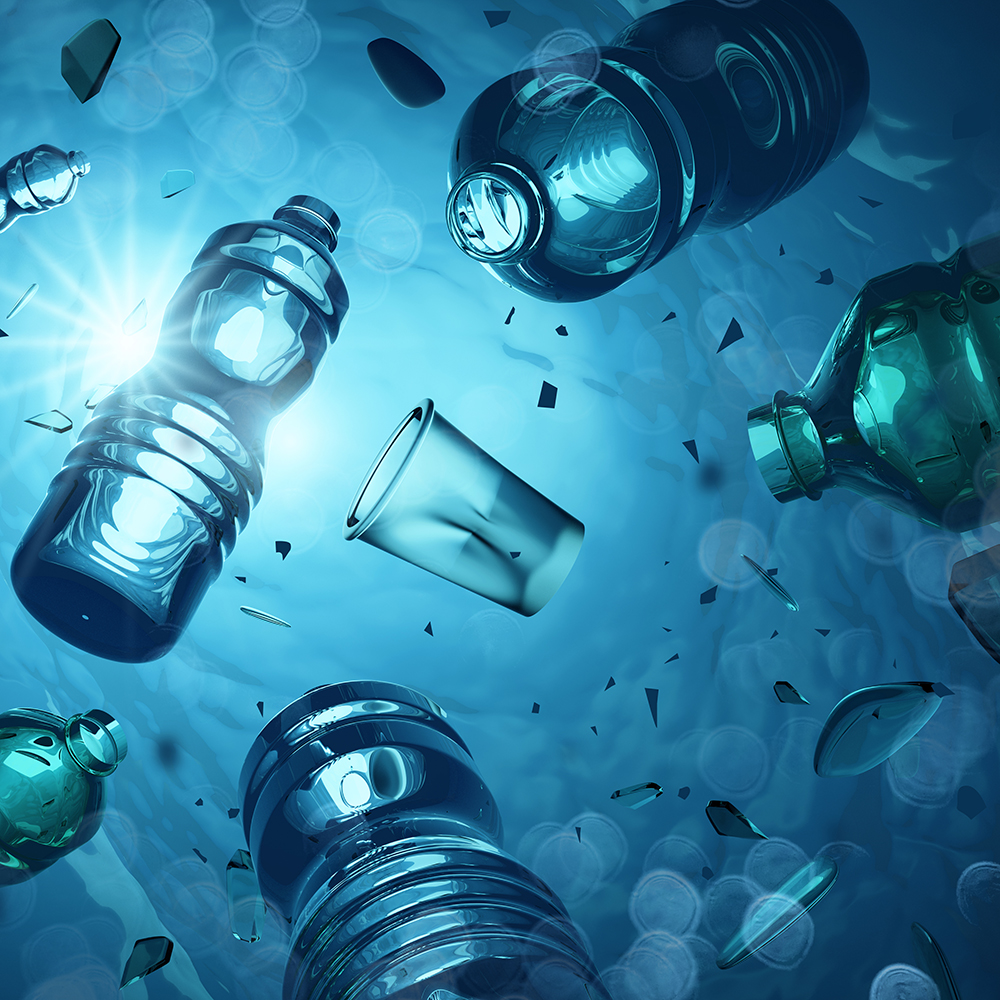
Non-recyclable Plastics
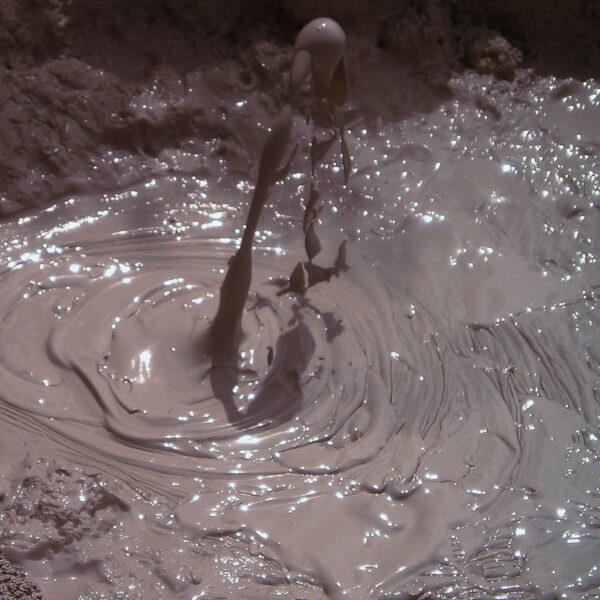
Sewage Sludge
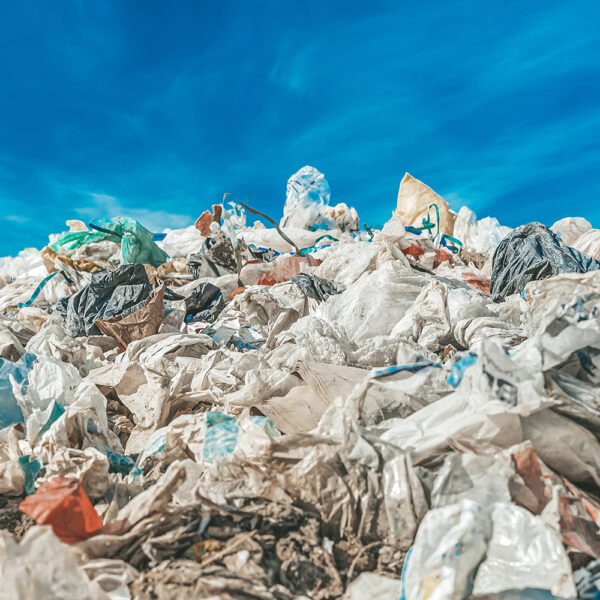
Municipal Waste
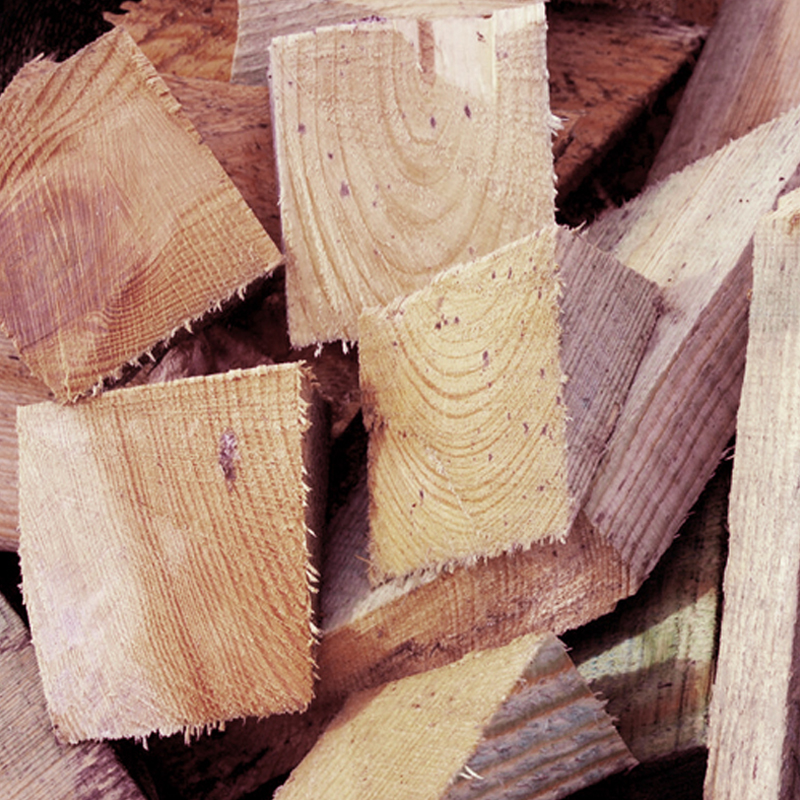
Waste Wood
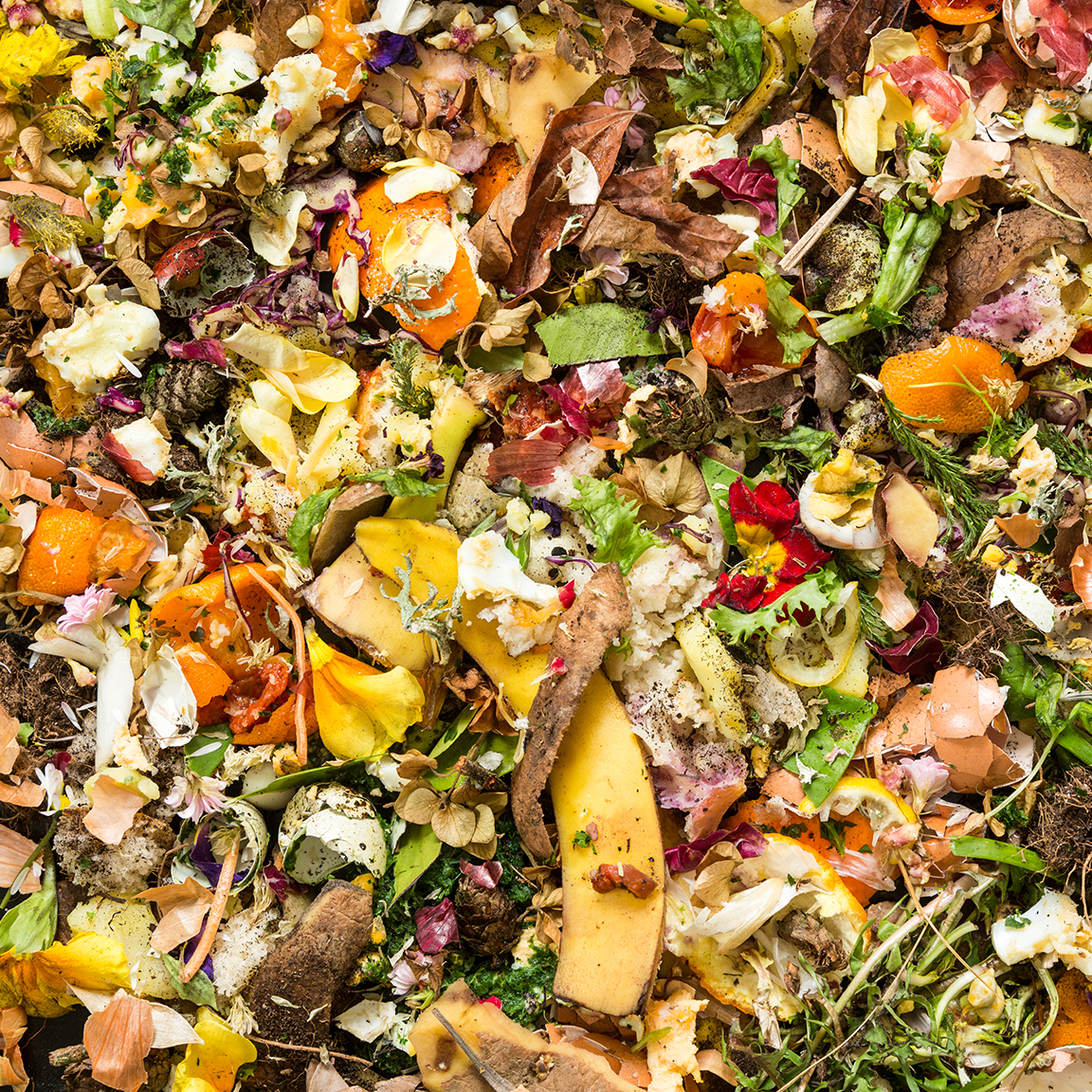
Biomass
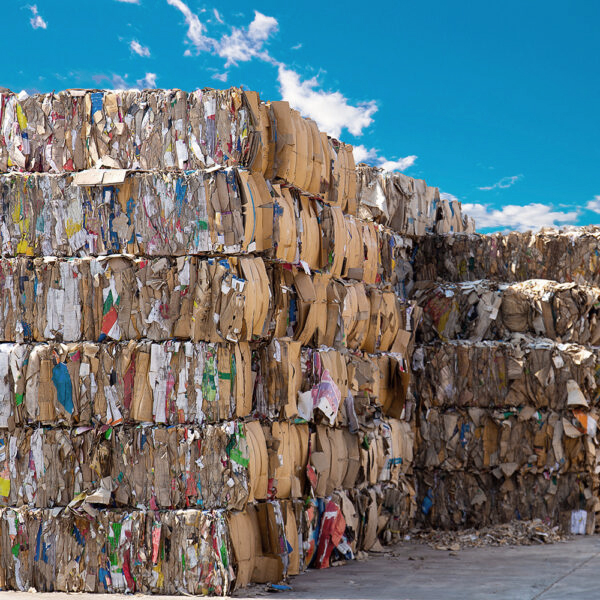
Paper & Cardboard
The SYNTHEC FUELS Solution
Processes for the Conversion of Waste and CO2 into sustainable Products
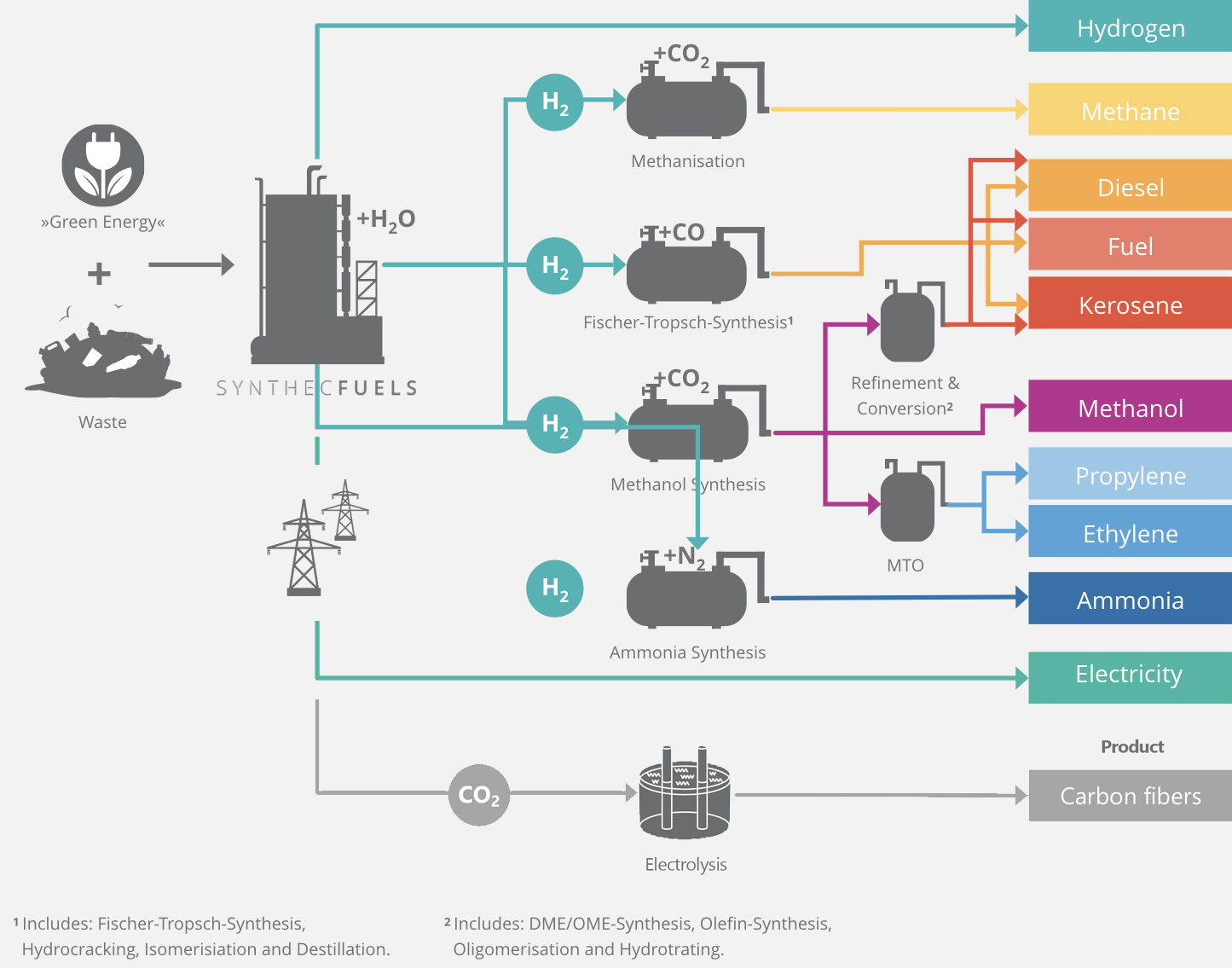
HYDROGEN | METHANE | DIESEL | FUEL | KEROSENE |
---|---|---|---|---|
Trucks & Heavy Traffic |
Trucks & Heavy Traffic | Trucks & Heavy Traffic | Cars | Air Traffic |
Communal Transport |
Communal Transport | Communal Transport | ||
Railway Traffic |
Process Heat Industry | |||
OIL Refineries |
Real Estate | |||
Steel Production |
||||
Process Heat Industry |
||||
Real Estate |
METHANOL | PROPYLENE | ETHYLENE | AMMONIA | ELECTRICITY |
---|---|---|---|---|
Chemical Industry | Chemical Industry | Chemical Industry | Chemical Industry | Cars & Light Traffic |
Cars & Light Traffic | Shipping Industry | Communal Transport | ||
Shipping Industry | Railway Traffic | |||
Steel Production | ||||
Process Heat Industry | ||||
Real Estate |
Synthec Fuels Hydrogen & Fuels – Reliably available
Synthec Fuels will produce sustainable, green Hydrogen with 7.500 – 8.000 Full-Load-Hours per Year
(Base Load Capability > 5.000 Full-Load-Hours)
The term Full-Load-Hour is a unit of measurement used to indicate the degree of utilization of a plant. Since plants do not usually run at full load all year round, but sometimes only operate at partial load or are shut down for maintenance. The maximum number of Full-Load-Hours per year is 8,760 hours (365 days with 24 hours each) and depending on the type of plant, weather conditions of the respective year and plant-specific restrictions.
Hydrogen Logistics
State-of-the-Art Hydrogen Storage Concepts have Significant Drawbacks
Compressed (CGH2)
160 – 750 bar
- Low storage density
- High capex and maintenance costs
- Large safety zones
or
Flammable Gas
Cryogenic (LH2)
–253 °C
- Very high energy consumption
- Very high capex and maintenance costs
- Not suitable for longer-term storage (e.g. boil – off)
- Large safety zones
Synthec Fuels’ Logistic Solution for Export
Liquid Organic Hydrogen Carrier (LOHC) enable a safe and efficient Transport of Hydrogen at ambient Conditions
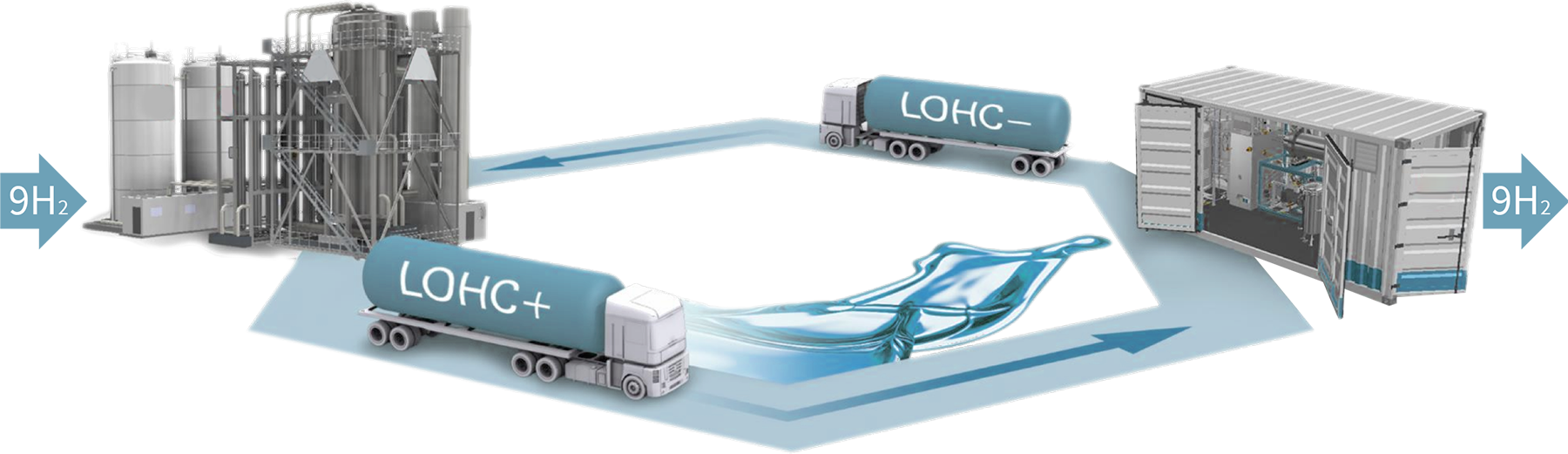
Hydrogenation
Exothermic – ca. 250 °C
25 – 50 bar
The LOHC technology
uses basic chemical processes to eliminate the
complexities of today’s hydrogen handling
Dehydrogenation
Endothermic – ca. 300 °C
1 – 3 bar
Low Cost and a highly flexible Supply Chain based on existing Fuel Infrastructure are Key to a full Commercial Roll-Out
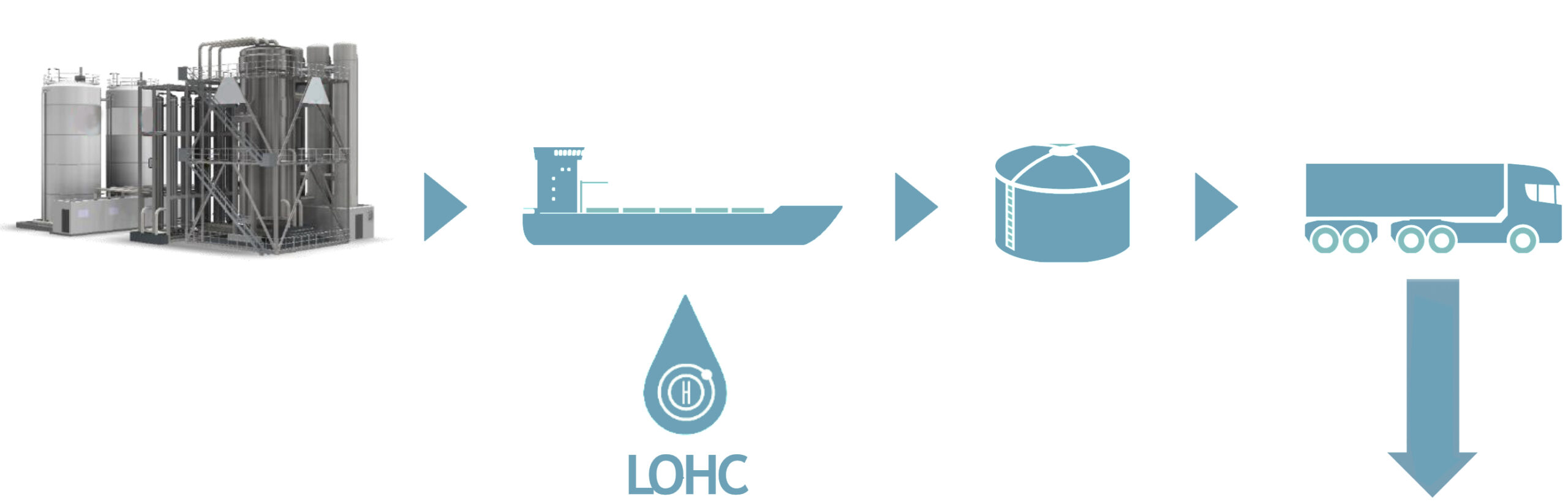
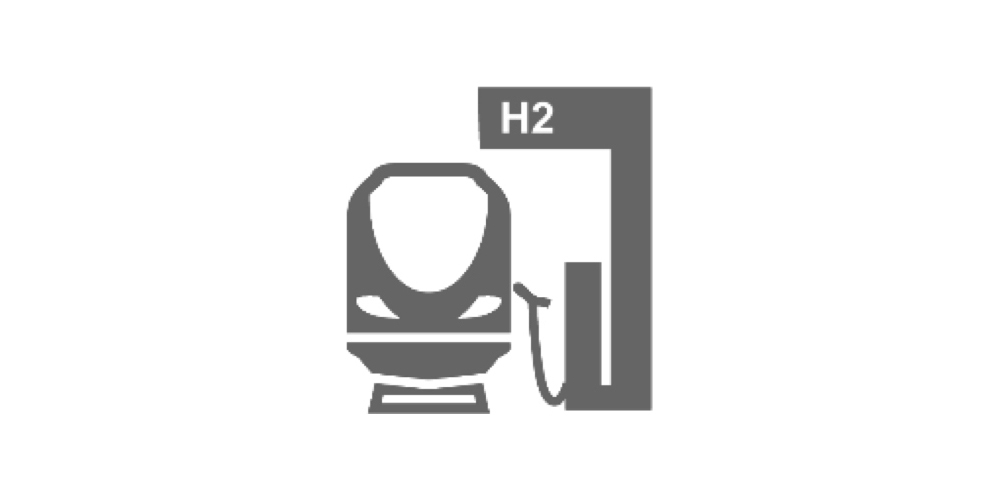
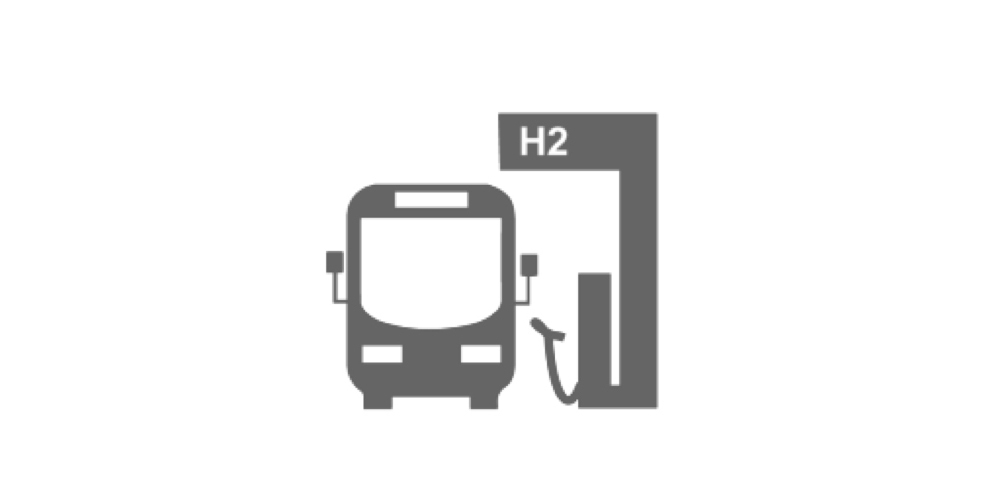
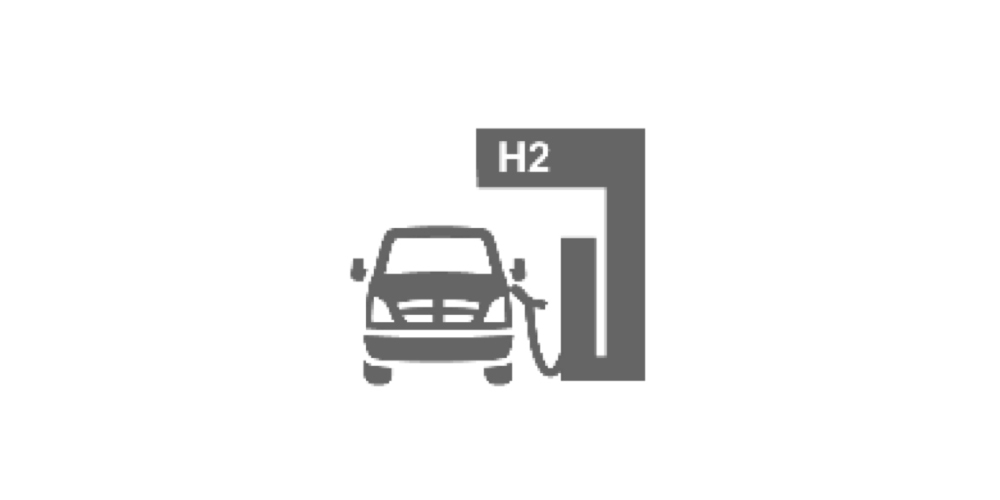
A single oil/LOHC tanker can fuel ~140 buses for over 2 years
Liquid Organic Hydrogen Carrier (LOHC) in comparison
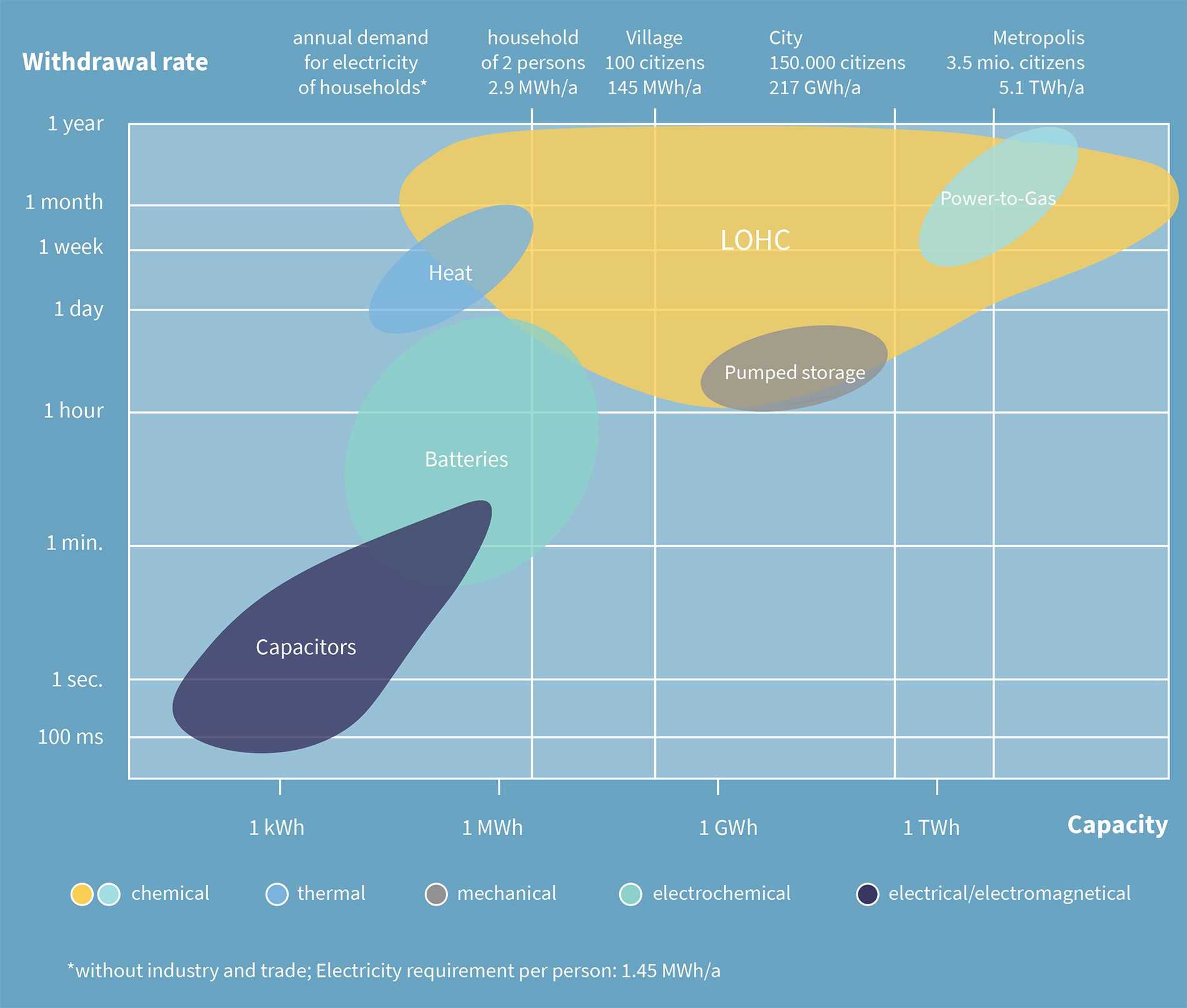